Konecranes at New Wisconsin Paper Mill
Konecranes has been chosen to supply nine cranes, including four automated roll storage cranes, for the first new paper mill built in Wisconsin in over 30 years. The order was booked in Q2 2019.
Leading global crane manufacturer Konecranes was selected by Green Bay Packaging as the lifting provider for a new $500 million, state-of-the-art facility that will be built on the company’s existing 38-acre site in Green Bay, WI. Green Bay Packaging produces recycled kraft paper products used in the food and beverage industry and other consumer products. The new mill will generate 685,000 tons annually, over double that of the current operation.
Konecranes was selected to supply the bridge cranes for the entire mill, including two identical SMARTON® cranes for the wet end and dry end of the paper machine, three CXT maintenance cranes, and four Autostore fully automated storage cranes whose software package will interface with the facility’s conveyor as well as other systems for warehousing and shipping. The cranes are rated for CMAA Class C/D service and are radio-controlled. They are also equipped with TRUCONNECT® Remote Monitoring, which collects key data points for crane maintenance planning and extended equipment life and is closely integrated to the yourKONECRANES® cloud-based customer portal, bringing crane maintenance information online for all asset managers to see.
“Konecranes and Demag have a leading position worldwide in automated storage and retrieval systems (ASRS) using cranes,” says Juergen Gieske, vice president, crane sales. “Since Konecranes and Demag joined their experiences and resources, we are able to put the best of both systems to work for our customers. One benefit of this merging of brands is our ability to leverage extension modules for our Autostore ASRS paper roll handling cranes to communicate with all other devices and technology associated with the customer’s manufacturing execution system (MES) – such as the conveyors, printers and shipping protocols.” Gieske also noted that overhead cranes using vacuum or mechanical roll lifter technology provide damage-free roll handling that is the densest by volume of any warehousing solution.
“The most common alternative to cranes is the use of manual operators driving lift trucks with roll clamp attachments,” Gieske said. “These clamps often result in roll damage, delayed shipments, unwanted costs and dissatisfied downstream customers. The lift trucks also require much more warehouse real estate to accommodate the aisle-ways required to navigate at floor level – not to mention the lift truck’s limited roll vertical stacking heights.”
But the ASRS is not the only impressive aspect of this installation. The SMARTON model wet-end and dry-end cranes are designed for a high moisture and high temperature environment, rated IP66 with many stainless steel features. Each crane features three top-running trolley hoists in capacities of 50/100/50 metric tons, plus two 10-ton auxiliary monorail hoists for additional material handling capabilities. This amounts to five trolley/hoists on each crane.
In addition, the two 92-foot-span SMARTON cranes are equipped with rotating paper roll spreader beams to handle the 12.5-foot diameter x 27-foot long parent rolls.
After the parent rolls are processed into smaller medium and linerboard rolls weighing up to 10 tons each, conveyors move them into one of two paper warehouse bays. Each bay is serviced by two 7-ton, 120-foot span, CMAA Class F, ASRS high-density warehouse cranes equipped with vacuum lifters that pick up the rolls and store them in vertical columns up to four rolls high. Bar coding allows each roll to be identified individually and scanned into the Warehouse Management System (WMS) Level Two (2) where the crane software is completely responsible for inventory and retrieval.
Green Bay Packaging’s Director of Logistics Frank Miller says that Konecranes automatic storage and retrieval system was a critical component for the new mill.
“There’s no way that we could store the amount of paper that we need to on our site without this Konecranes technology,” says Miller. “Konecranes ASRS enabled us to store more paper in a much smaller area than either a standard warehouse or high density storage rack type application. A high density rack application is linked to the size of the roll you are going to manufacture, and there’s not a lot of flexibility if your roll sizes change in width or diameter. Konecranes application allows us the flexibility to have different trim widths, high density and high speed, and we needed all three of these things.”
Green Bay Packaging’s manufacturing protocol calls for the Autostore ASRS cranes to operate 24 hours a day, 7 days a week. They will receive rolls into the warehouse, then retrieve them and place them onto conveyors to be delivered to the shipping docks. There, they will be removed by lift trucks and loaded onto trucks or rail cars.
“Initially we considered a solution that picked up rolls with manual grippers, using a clamp,” says Miller. “But the Konecranes team recommended a vacuum lifter. It reduces the distance between the rolls from eight inches to four inches, giving us higher density storage and 20 percent more speed. That was a very important feature, and the vacuum lifters are able to maintain a very high level of safety. If there is a power failure it can maintain a roll suspended up to 45 minutes.”
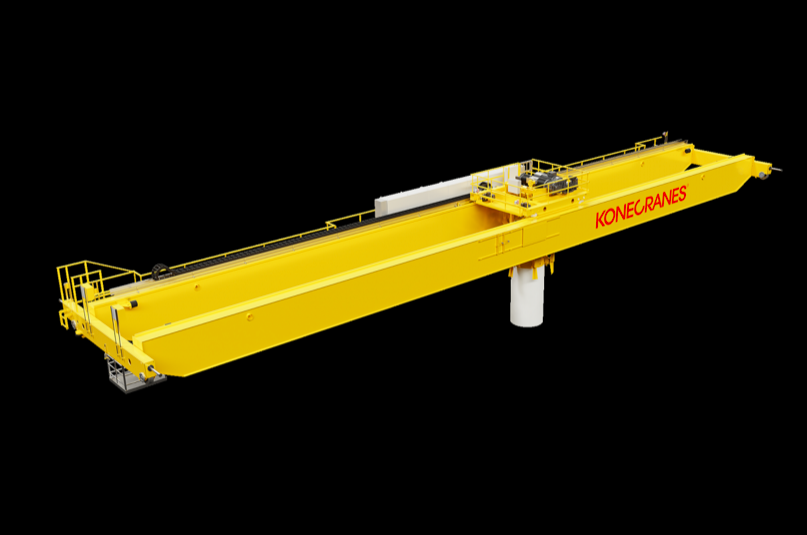
Konecranes was selected to supply the bridge cranes for the entire mill.
Green Bay Packaging also purchased three maintenance cranes from Konecranes proven CXT series, which will be key to the upkeep and reliability of the plant. These include a 5.5-ton core-handling crane, a 16.5-ton vacuum blower crane and a 16.4-ton shop area crane. All three are built with high moisture protection and IP66 stainless steel electrical designs.
Konecranes will also provide the runway rail, power supply and installation for the nine cranes. Commissioning, load testing and operator training round out the project’s scope, which is expected to be fully operational in the spring of 2021.
Green Bay Packaging’s Frank Miller and Warehouse Area Project Manager Joseph VerVelde visited Konecranes headquarters in Finland with their team as part of their research for this state-of-the-art project, and toured multiple sites in Europe where Konecranes roll storage technology was making a difference for paper producers there.
“We saw that the Autostore ASRS provided a high level of integration in the warehouse, using the cranes, conveyors and warehouse management system to manage the entire put-away, storage and pick process,” said Miller. “We felt that Konecranes was the primary player in this technology, and had the global footprint from an engineering and resource standpoint to handle a project of this magnitude. That gave us a lot of confidence.”