MacGregor GravityVibe
MacGregor, part of Cargotec, has launched a new and augmented gravity self-unloading system that will allow bulk carriers to deliver a wider variety of cargo, in greater volume.
The new system, the MacGregor GravityVibe, deploys a patent-pending vibrating unloader to reduce internal friction and ease the discharge of coarse materials such as wood chips from the cargo hold.
While the automated unloading sequence remains a gravity-based operation, the MacGregor GravityVibe includes vibrating panels to shift the remnants or break the ‘bridges’ that form when coarse material sticks together to block the outlet. Crucially, the vibrating panels are isolated from the hull structure – using a solution from MacGregor on which a patent is pending – to minimise the transfer of vibrations and noise to other parts of the vessel.
In contrast with a standard gravity self-unloading configuration, where slope angles range from 35 to 60 degrees depending on the material, the MacGregor GravityVibe can discharge various cargo types with slope angles of just 15–20 degrees. Since steep slope angles limit hold volume, the system therefore increases not only the variety of cargo types a vessel can handle but also its cargo capacity. The additional capacity also translates into lower carbon dioxide emissions per carried tonne of cargo.
“Bulk carrier cargo holds are typically designed to handle a specific kind of material, meaning the ship owner is somewhat limited in the type of assignments they can take on,” said Mikael Hägglund, Sales Manager, Self-unloading systems and Cranes, MacGregor.
“The MacGregor GravityVibe overcomes these limitations to afford owners greater flexibility when taking on new contracts, and it also boosts earning potential and environmental performance by optimising cargo capacity.”
Whereas large sized conventional self-unloaders feature two longitudinal and two transfer conveyors, the MacGregor GravityVibe’s low slope angles also mean that it functions with just one longitudinal conveyor. With fewer components installed, the required maintenance and spare-parts will be low when compared with conventional self unloading systems. The streamlined set-up also minimises spillage and the need for cleaning, meaning less work and improved safety for crew. With its increased efficiency and reduced complexity, the MacGregor GravityVibe solution provides a highly cost effective alternative to traditional solutions.
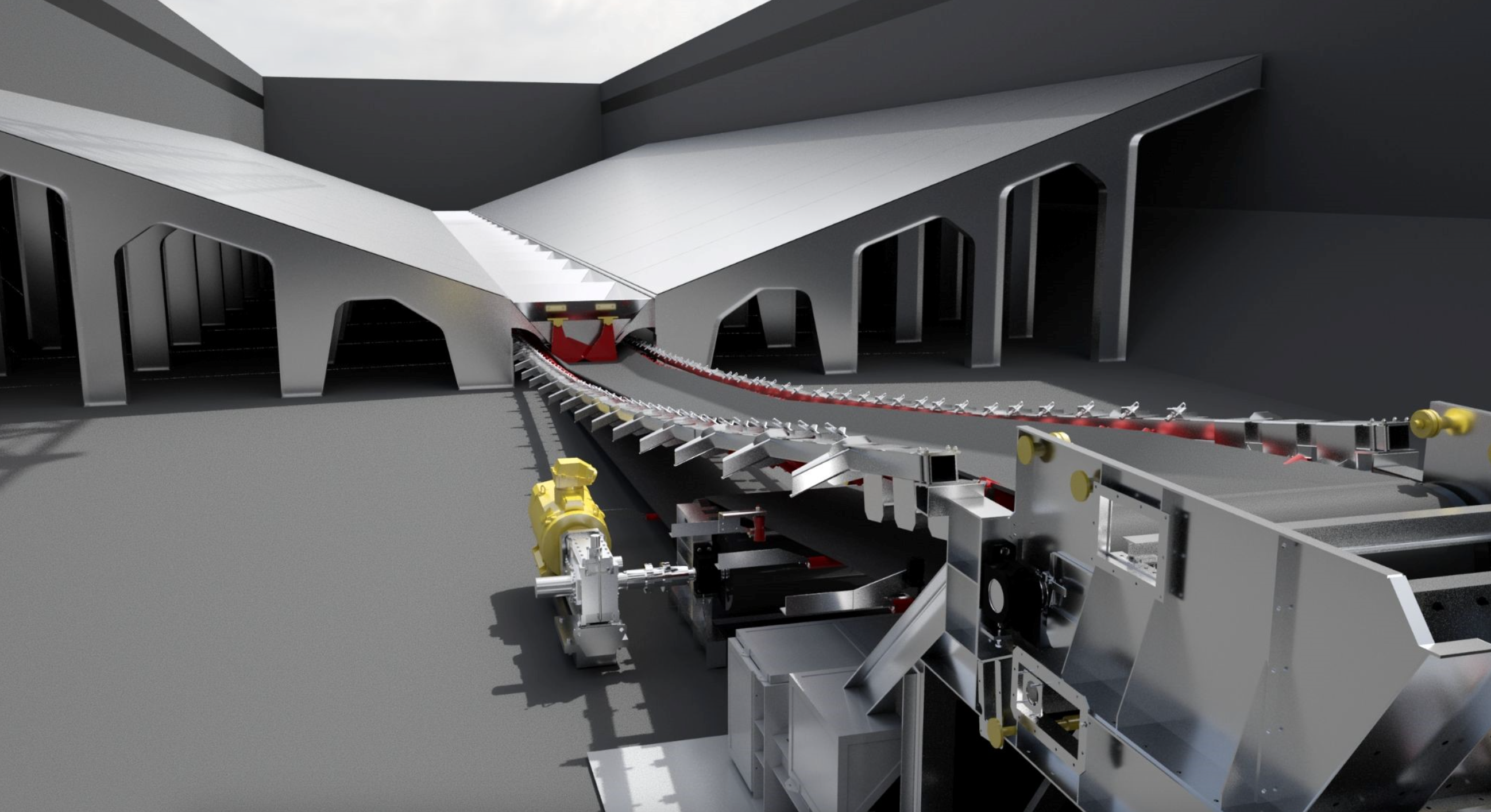
MacGregor GravityVibe deploys a patent-pending vibrating unloader to reduce internal friction and ease the discharge of coarse materials such as wood chips from the cargo hold.
“As the culmination of decades of experience in self-unloading systems and years of targeted research, the MacGregor GravityVibe is our most advanced self-unloader yet,” said Tomas Wallin, Senior Product Owner, Self-Unloaders, MacGregor.
“We developed the system according to established best practice, using textbook understanding of material behaviours in combination with a decisive innovation on how to handle cargo types with different properties. We have also tested it in collaboration with leading research centres and technology area experts.”
- MacGregor will be offering customers the opportunity to validate the GravityVibe’s handling of their chosen materials in full-scale mock-up demonstrations at the company’s test facilities.